Packaging waste is a growing environmental concern, especially in the food industry, where single-use plastics dominate. Moving toward reusable packaging offers a promising solution, but implementing such systems introduces significant logistical and economic challenges. At R3PACK, we are using advanced optimisation models to design and evaluate sustainable reuse networks, balancing economic costs and environmental impacts.
What is an optimisation model, and why is it important?

An optimisation model is a mathematical tool used to identify the best solution to a complex problem under specific constraints. In the context of packaging reuse closed-loop networks, it helps decision-makers answer critical questions, such as:
Where should washing and sorting facilities be located to minimise transportation costs?
How should packaging be routed through the network to balance operational efficiency and environmental impact?
What are the trade-offs between reducing emissions and controlling costs?
The optimisation model developed within R3PACK project focuses on the design of a closed-loop system, where packaging flows from producers to consumers and back for cleaning and reuse. It incorporates variables like packaging return rates, transportation distances, and facility capacities, aiming to minimise costs and emissions while ensuring a reliable and resilient network.
Advantages of optimisation models:
Holistic perspective: They account for the entire system, from packaging production to consumer returns and reuse processes.
Quantitative insights: Models provide precise, data-driven results that help stakeholders understand the implications of different choices.
Scenario analysis: By simulating various scenarios, such as changes in return rates or material costs, models enable informed decision-making.
Challenges and limitations:
Data dependency: Optimisation models require large amounts of accurate data, including transportation costs, packaging weights, and return patterns. Incomplete or imprecise data can compromise results.
Computational complexity: Solving large-scale models, especially those involving many actors and variables, can be time-intensive and requires advanced computational tools.
Despite these challenges, optimisation models are indispensable for designing reuse networks, as they allow for systematic evaluation of trade-offs and support long-term sustainability goals.
Who are the key players in a reuse network?
Designing a successful reuse system involves coordinating multiple actors, each with specific roles and challenges:
Packaging producers: Responsible for manufacturing durable, reusable containers, often requiring investments in new production lines and materials.
Food packagers: Fill and seal reusable packaging with food products. They must adapt operations to accommodate reusable containers, which may differ in size and material from single-use alternatives.
Retailers and distribution centres: Handle the distribution of packaged food to consumers and manage the return of empty containers. Their location and capacity play a crucial role in optimising the network.
Consumers: Their willingness to return packaging significantly influences the system’s efficiency. Incentives like deposit-refund schemes are often used to encourage participation.
Washing and sorting facilities: Ensure that returned containers meet hygiene and quality standards. These facilities are critical for maintaining the safety and functionality of reusable packaging.
Transportation providers: Manage the movement of packaging between facilities, with a focus on minimising costs and emissions.
Each of these actors introduces variables and constraints into the optimisation model, highlighting the complexity of reuse networks.

The logistics of reuse: balancing costs and emissions
One of the core findings of the R3PACK project is the dynamic relationship between economic costs and environmental impacts. While traditional logistics often aligns these goals, reuse systems require careful balancing:
Costs: Additional transportation and cleaning processes can increase operational expenses. Investments in infrastructure, such as washing facilities and reverse vending machines, also contribute to upfront costs.
Impacts: Reuse systems achieve significant environmental benefits by reducing the demand for new packaging. However, these gains depend on efficient logistics and high return rates to offset the emissions from additional transportation.
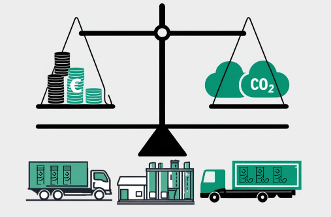
Logistics is a central component of reuse networks, as it determines how packaging flows through the system. Unlike traditional supply chains, which primarily focus on delivering products to consumers, reuse networks also manage the reverse flow of packaging back to facilities for cleaning and redistribution. This added complexity introduces new cost and environmental considerations.
In general, economic and environmental goals align in logistics: shorter routes and efficient operations typically reduce both costs and emissions. However, reuse networks present unique challenges:
Increased transportation stages: While reuse reduces the need for new packaging, it requires additional transportation to return used containers from consumers to washing and sorting facilities. This can increase fuel consumption and emissions, particularly in regions with dispersed populations.
Extending the lifecycle of reusable packaging: The environmental benefits of reduced production in reusable packaging systems grow significantly with the number of use cycles a container achieves. The key challenge, therefore, is increasing the number of reuse cycles to distribute the production footprint effectively, thereby offsetting the additional emissions from reverse logistics. Achieving this requires strong consumer engagement to ensure high return rates and the design of durable packaging materials capable of withstanding repeated use.
The R3PACK sensitivity analysis revealed that these trade-offs depend heavily on key factors, such as consumers’ willingness to return the packaging and reusable food containers durability. For example, a higher return rate reduces the need for new packaging, making the system more environmentally efficient despite increased transportation. Similarly, improving packaging durability lowers the overall cost and impact of the system by reducing breakage and disposal rates.
Through sensitivity analyses, R3PACK has demonstrated how small changes in system parameters—such as consumer behavior or facility locations—can strongly affect these trade-offs. For example, placing washing facilities closer to urban centres reduces both costs and emissions by minimising transportation distances. Similarly, increasing consumer participation in packaging returns reduces the need for new production, amplifying environmental benefits.
Building a sustainable future
The R3PACK project underscores several critical insights for creating effective reuse networks, highlighting the importance of strategic facility placement, consumer engagement, and durable packaging design. The location of washing and sorting facilities can significantly influence both transportation costs and emissions, while durable packaging reduces the need for replacements, enhancing both economic and environmental sustainability. At the same time, encouraging consumers to return packaging through convenient systems, like reverse vending machines, is crucial to ensure high return rates and maintain the flow of reusable containers. Balancing these factors requires careful consideration of trade-offs, such as managing the higher transportation costs of reuse systems against the significant reductions in emissions achieved by avoiding the production of new packaging.
The ultimate challenge lies in reconciling the diverse perspectives of all stakeholders involved—packaging producers, retailers, policymakers, and consumers—each with their own goals and priorities. Achieving this balance necessitates an integrated, holistic approach that evaluates the entire system, considering economic, environmental, and logistical dimensions simultaneously. Mathematical optimisation tools and sensitivity analysis enable the development of tailored recommendations and best practices for the design of reuse networks and the optimisation of their logistical operations. These tools aid detailed what-if analyses, allowing stakeholders to explore the implications of different decisions and uncertainties, and to identify the most effective strategies for achieving sustainability goals. This approach not only ensures that reuse networks are efficient and resilient but also supports informed decision-making across the supply chain, driving systemic change and advancing sustainability in the food sector.
Comments